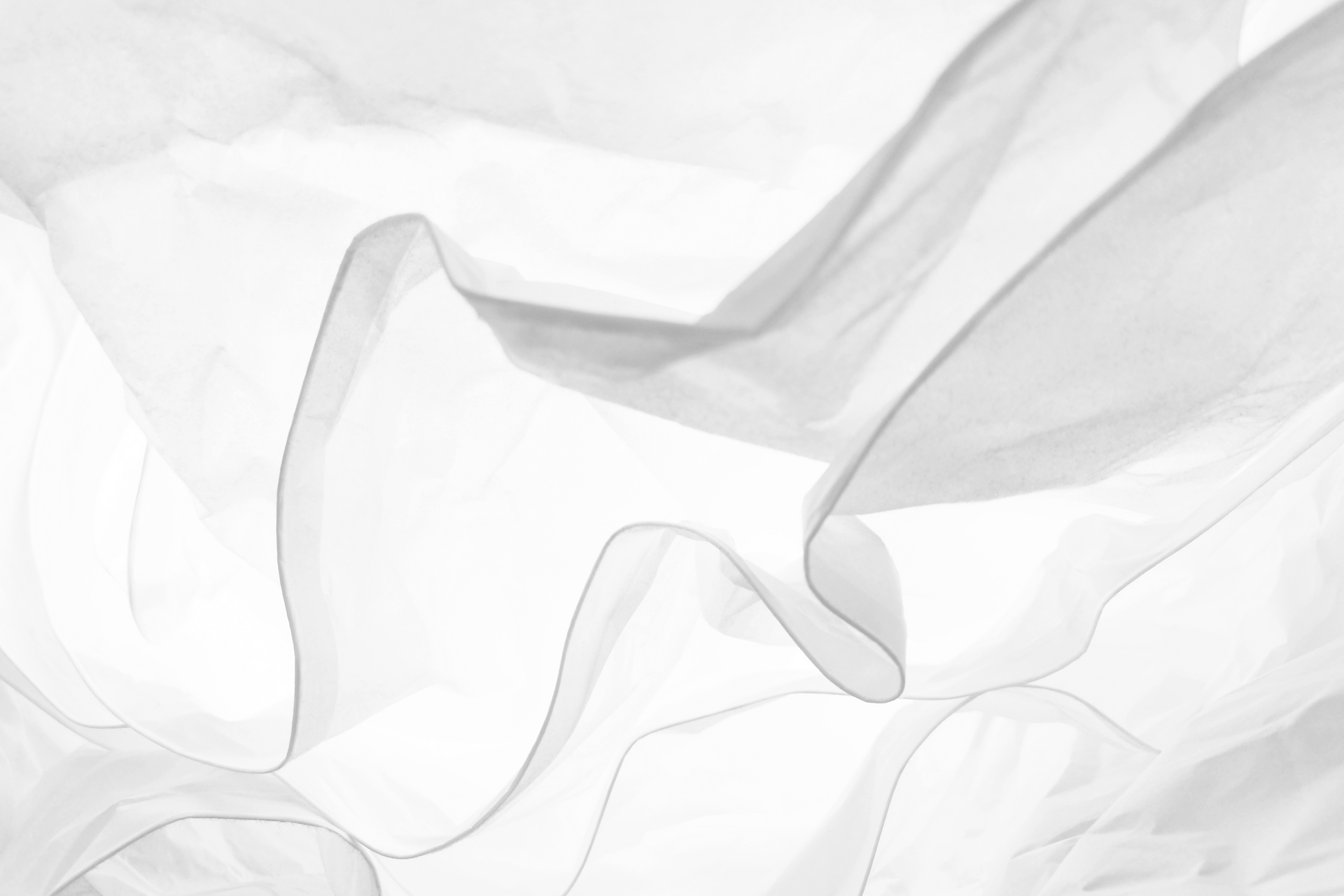
Sustainable Technologies in Textile Machinery.
​
Sustainable technology refers to the technology which caters the needs of the present without compromising the ability of future generation to meet their own needs. It enables more valuable use of the natural resources & greatly reduced ecological impact among other technological benefits. Though sustainable technology deals with energy efficiency, reduction in pollution, use of renewable sources, it should also be economically sustainable!

More than 2000 types of dyes, chemicals & other auxiliaries are being used in Textile Industry.

The World Bank estimates that almost 20% of global industrial water pollution comes from the treatment and dyeing of textiles

A single T-shirt made from conventional cotton requires 2700 liters of water and a third of a pound of chemicals to produce.

Cotton production accounts for 2.6% of annual global water usage.
Trending Machinery



Exhaust Piece Dyeing
LOTUS machine which is the world’s first long tube machine to operate using to the original aerodynamic principle. The objective of the development was to create a system that would be especially suitable for the wet processing of delicate, easily creased, cellulose and synthetic fibre knits and wovens with a high percentage of elastane fibre, which are used in the lingerie, sport, leisure and swimwear segments. Benefits: Resource benefits focus on ultra-low liquor ratio 1:2 to 1:5 with associated reduction in water demand, effluent volume and loading from reduced salt consumption when reactive dyeing and a reduced energy requirement. FONG’S have further refined their JUMBOFLOW machine with Advanced Intelligent Rinsing (AIR) with the option of a conductivity measurement to detect when the concentration of electrolyte has reduced after reactive dye processing to a concentration where the rinsing is transferred to the soaping stage, thereby optimising water consumption.



Cold Pad Batch Dyeing
For vertical knitted fabric operations there is a renewed interest in reactive dye application by cold pad batch application due to the lower consumption of water and reduced effluent loading, with a claimed reduction in variable costs of between 15 and 30%. The resultant fabric has a much cleaner stitch definition due to no surface abrasion, and to produce a similar g/sq.m fabric as exhaust dyeing, an increase in stitch density should be considered at the knitting stage if the Cold Pad Batch application route is in ended. Benefits: Developments in machine design are mostly for open width processing using sophisticated auto-centre and edge uncurling devices but also include dosing pumps, low-liquor troughs and configurations to allow dye application in the nip as well as in the low-liquor trough.Also on modern pad rollers the pressure can be adjusted across the full width to allow uniform liquor pick-up to eliminate side-centre-side variation.



Monforts Eco Applicator
An excellent example highlighting how the Blue Competence concept can influence the R&D activities is the Matex Eco Applicator; a unit which significantly reduces the initial moisture content before the drying process. The challenge of sustainability is to save natural resources without compromising production quality of the final products. The ECO Applicator ensures reduced energy consumption, faster drying and higher productivity compared with standard equipment such as padding systems. Benefits: Reduction the liquor pick up, which is the means of operation of the Monforts Matex ECO Applicator, results in less evaporation heat and lower operating costs. With the ECO Applicator, the liquor is not applied to the fabric by dipping it through a trough but by using steel rollers which transfer the required amount of liquor onto the fabric. With lower waste water contamination the application unit becomes a resource-conserving alternative to padding.